서 론
노천광산에서 천공, 발파, 적재, 운반작업 등으로 구성된 생산 공정을 효과적으로 계획하고 관리하는 것은 매우 중요하다(Hartman and Mutmanski, 2002; Choi and Nieto, 2011a, Choi and Nieto, 2011b). 생산 시스템의 설계에 따라 광산의 생산성과 이익이 크게 달라질 수 있기 때문이다. 특히, 일반적으로 광석 및 폐석 운반작업에 투입되는 비용이 전체 생산 비용의 절반 이상을 차지하기 때문에 운반시스템의 효율적으로 설계하고, 운영하는 것은 매우 중요하다(Alarie and Gamache, 2002).
효율적인 운반시스템 설계와 운영을 위해서는 운반작업에 투입되는 장비들의 종류, 수, 성능을 최적화할 필요가 있다(Choi et al., 2016). 이를 위해 해외에서는 운반시스템에 투입되는 장비의 조합과 운영방식을 최적화할 수 있는 시뮬레이션 연구가 활발히 진행되어 왔다(Bonates, 1996; Temeng, 1997; Aksoy and Yalçin, 2000; Niemann-Delius and Fedurek, 2004; Ibarra, 2015; Amin et al., 2017; Kuznetsov and Aksyonov, 2019). 국내에서도 트럭의 배차방식, 고장 발생 가능성, 파쇄기의 처리용량 등 다양한 요인들을 고려하여 트럭-로더 운반시스템을 시뮬레이션할 수 있는 기법 및 프로그램 개발 연구가 수행되었다(Choi, 2011; Park and Choi, 2013; Park et al., 2014a, Park et al., 2014b; Park et al., 2014c; Choi et al., 2016; Park et al., 2016; Lee and Choi, 2018).
기존 연구에서 사용된 시뮬레이션 프로그램들은 두 가지 한계점을 갖는다. 첫째, 시뮬레이션이 종료된 후 운반시스템 성능을 나타내는 주요 지표 값들(광석 생산량, 장비 이용율, 지연시간 등)만 확인할 수 있었다. 따라서 시뮬레이션이 진행되는 동안은 시간에 따라 변화하는 주요 지표 값들을 사용자가 확인할 수 없었다. 둘째, 시뮬레이션 결과의 가시화를 위해서는 시뮬레이션이 종료된 후 다른 프로그램과 연동하는 과정이 필요했다. 이러한 한계들로 인해 사용자는 운반작업의 효율이 저하될 때 어떤 부분에서 문제가 발생하는지 직관적으로 판단할 수 없는 문제가 있었다.
본 연구의 목적은 노천광산 트럭-로더 운반시스템의 시뮬레이션을 통해 시간에 따라 변화하는 운반시스템의 주요 성능 지표 값을 확인하고, 작업 상황을 실시간 가시화할 방법을 제시하는 것이다. 이를 위해 국내 석회석 노천광산을 대상으로 애니로직(Anylogic) 소프트웨어를 이용하여 새로운 트럭-로더 운반시스템 시뮬레이터를 개발하였다. 개발된 시뮬레이터를 이용하여 작업 시간에 따른 운반시스템의 주요 성능 지표 값을 예측하고, 현장의 운반작업 상황을 3차원으로 가시화하였다. 일부 작업 시간에 대해서는 현장의 실제 운반작업 촬영 영상과 시뮬레이션 가시화 결과를 비교하였다.
본 연구에서는 노천광산의 트럭-로더 운반시스템의 시뮬레이션을 위해 애니로직 소프트웨어를 이용하였다. 애니로직 소프트웨어는 에이전트 기반 시뮬레이션, 이산사건 시뮬레이션, 시스템 다이내믹스 시뮬레이션이 모두 가능한 다중 기법 시뮬레이션 소프트웨어이다(Anylogic, 2020). 에이전트 기반 시뮬레이션은 사건의 발생 후 객체의 변화를 파악할 수 있으며, 이산사건 시뮬레이션은 순차적인 사건의 흐름을 고려한 모델링이 가능하다. 또한, 시스템 다이내믹스 시뮬레이션은 객체 및 사건에 대한 세부적인 설정 없이 모델의 일반적인 결과를 파악할 수 있다.
애니로직 소프트웨어는 시뮬레이션 진행 상황과 결과를 실시간으로 가시화할 수 있고 시뮬레이션 동안 발생하는 문제점을 직관적으로 확인할 수 있으며, 공장설계(Lee, 2019), 도시설계(Chen et al., 2019), 도로설계(KUKLOVÁ, and PŘIBYL, 2019), 시설 관리(Bauer et al., 2019), 물류 관리(Ren et al., 2019), 보안 시스템 분석(Tun et al., 2019), 전략 개발(Frolova et al., 2019), 승객 관리(Dubroca-Voisin et al., 2019)와 같은 다양한 목적으로 사용되고 있다.
애니로직 소프트웨어의 장점을 정리하면 다음과 같다.
∙ 시뮬레이션 언어를 배우지 않아도 사용 가능
∙ 실제와 유사한 객체 크기나 모양으로 구현 가능
∙ 자동 시각화 기능 제공
∙ 2차원과 3차원 시각화 기능 제공
∙ 통계 분석 기능 제공
∙ Java 언어를 이용하여 시뮬레이션 확장 가능
∙ 다른 사람들과 cloud를 통해 시뮬레이션 결과 공유 가능
애니로직 소프트웨어를 이용한 시뮬레이션 개발은 다음 절차에 따라 수행된다. 먼저 시뮬레이션 모델을 만들기 위해 장소, 길, 객체 등을 설계한다. 다음으로 시스템의 운영 절차에 맞게 시뮬레이션 모식도를 작성한다. Fig. 1은 애니로직 소프트웨어의 사용자 인터페이스를 보여주며, A는 컴포넌트 집합 창, B는 디자인 창, C는 속성 창을 나타낸다. 컴포넌트 집합 창에는 차, 길, 건물, 컨테이너, 배, 실내장식, 나무, 사람과 같은 객체 블록들이 나열되어 있으며, 사용자는 원하는 객체 블록을 드래그하여 디자인 창에 놓을 수 있다. 디자인 창에서는 객체 동작 블록들을 순서에 맞게 배열하여 모식도를 생성할 수 있고, 시뮬레이션 결과를 편리하게 보기 위해 대시보드를 따로 디자인할 수 있다. 속성 창에서는 객체의 개수, 모양, 이름 등을 설정할 수 있으며, 플로차트 내 객체 동작 블록들의 작업 소요 시간, 객체 대기 장소 등을 설정할 수 있다.
연구방법
연구지역 및 현장조사
본 연구에서는 쌍용양회에서 운영하는 신기 사업소 5지구의 석회석 노천광산을 연구지역으로 선정하였다. 이 광산은 강원도 삼척시 신기면(37°21′33″N, 129°3′4″E)에 위치하며, 연간 약 750만 톤의 석회석 광석을 생산하고 있다. Fig. 2는 연구지역의 위성사진을 보여준다. 연구지역의 트럭-로더 운반시스템은 2곳의 적재지점과 1곳의 파쇄장으로 구성되어 있다.
본 연구에서는 시뮬레이션 알고리즘 설계와 시각화를 위해 현장 조사 당시 실제 생산작업이 이루어졌던 작업장의 적재지점을 대상으로 사례연구를 수행하였다. Fig. 3은 연구지역 트럭-로더 운반시스템에서 이루어지는 단위 운반작업을 보여준다. 장비들의 단위 작업 시간과 관련한 인자 값들은 스톱워치를 이용하여 16회 동안 반복적으로 측정되었으며, 시간 인자 값들을 평균±표준편차 형태로 표시하였다.
Table 1은 연구지역의 트럭-로더 운반시스템에 투입되는 장비들의 제원과 현장 조사를 통해 측정된 시간 인자 및 경제적 인자 값을 보여준다. 트럭의 이동 시간은 공차 상태와 실차 상태에서 같다고 가정하였다.
Table 1. Specification of equipments, time parameters and economic parameters required for the truck-loader haulage simulation
시뮬레이션 모델 개발
트럭-로더 운반시스템의 알고리즘은 Suboleski(1975)가 제안한 트럭 순환 시간 이론에 근거하여 설계되었다.
$$\mathrm{TCT}=\mathrm{STL}+\mathrm{LT}+\mathrm{TL}+\mathrm{STD}+\mathrm{DT}+\mathrm{TE}+\mathrm{AD}$$ | (1) |
식 (1)에서 TCT(Total Cycle Time)는 총 운반작업 시간, STL(Spotting Time at Loader)은 대기 열에서 나온 트럭이 적재 장비까지 접근하는 시간, LT(Loading Time)는 광석 적재 시간, TL(Travel time of a Loaded truck)은 광석을 실은 트럭이 적재지점에서 파쇄장까지 이동하는 시간, STD (Spotting Time at Dumping area)는 파쇄장에 도착한 트럭이 광석 투하지점까지 접근하는 시간, DT(Dumping Time)는 트럭의 광석 투하 시간, TE(Travel time of an Empty truck)는 트럭이 파쇄장에서 적재지점까지 돌아오는 데 걸리는 시간, AD(Average Delay time)는 트럭이 적재 장비의 사용이 가능해질 때까지 적재지점에서 대기해야 하는 지연시간과 파쇄기의 사용이 가능해질 때까지 파쇄장에서 대기해야 하는 지연시간을 포함한다.
Fig. 4는 광산 현장 상황과 위의 트럭 순환 시간 이론을 적용하여 설계한 트럭-로더 운반시스템 시뮬레이션 알고리즘의 순서도를 보여준다. 각 트럭은 지정된 적재장으로 이동하여 석회석 광석을 파쇄장까지 운반하도록 설계하였다. 알고리즘 설계를 위해 STL, LT, STD, DT는 현장 조사를 통해 측정된 소요 시간의 통계값을 이용하였고, TL, TE는 적재장과 파쇄장까지의 경로와 트럭의 속도를 고려하여 임의의 값으로 설정했다. AD는 적재장의 로더를 이미 다른 트럭이 이용하여 트럭이 대기하는 경우, 파쇄장에서 덤핑하기 위해 대기하는 경우, 파쇄기 용량 부하 등 원인에 따라 다르게 설정될 수 있다.
트럭-로더 운반시스템의 효율성을 비교하기 위해 장비의 이용율과 하루 평균 수익을 계산하였다. 장비의 이용율은 운반시스템 내 장비 이용 시간 중 작업 대기 및 지연시간(non-cycle time)을 제외한 실제 장비 이용 시간(In-cycle time)만을 고려해 계산했다. 하루 평균 수익은 Park and Choi(2013)에 근거하여 다음 식을 통해 계산하였다.
$$\mathrm{ADP}=(\mathrm{NH}\times\mathrm C)\times\mathrm P-(\mathrm{TC}\times\mathrm{NT})-(\mathrm{LC}\times\mathrm{NL})$$ | (2) |
여기서 ADP(average daily profit)는 하루 평균 수익(USD/ day), NH(number of haulage operation)는 트럭의 운반작업 횟수, C(capacity of truck)는 트럭의 용량(ton), P(price per ton of ores)는 석회석의 판매가격(USD/ton), TC(truck’s operation cost)는 트럭의 운영비용, NT(number of trucks)는 트럭 수, LC(loader’s operation cost)는 로더의 운영비용(USD), NL(number of loaders)은 로더의 수를 의미한다.
시뮬레이션 모델의 구현을 위해 연구지역의 광석 생산 설비를 고려하여 Fig. 5와 같이 시뮬레이션 레이아웃을 설계하였다. Fig. 6은 애니로직 소프트웨어상에서 설계된 시뮬레이션 모식도를 보여준다. Fig. 4에서 제시한 트럭의 작업 흐름 순서를 반영하여 모식도를 작성하였다. 적재장에서 발생하는 트럭의 대기시간을 최소화하기 위해 첫 번째 트럭이 적재장에 도착하면 두 번째 트럭이 출발한다고 가정하였다. 즉, 시뮬레이션이 시작하면 트럭은 파쇄장을 출발하여 적재장에 도착하고, 이어 두 번째 트럭이 파쇄장을 출발한다. 석회석 광석을 실은 트럭은 파쇄장으로 이동하고 파쇄기를 이용할 수 있으면 대기하지 않고 이용하고 이용하지 못한다면 대기한다. 파쇄기의 이용이 끝난 트럭은 다시 적재장으로 향한다. 앞선 트럭이 로더를 이용하고 있다면 트럭은 적재장에서 대기한다.
연구결과
각 적재장에 배차되는 트럭의 대수를 달리 설정하면서 시뮬레이션을 수행하였다. 신기 사업소의 트럭 보유 대수(8대)를 고려하여 각 적재장에 배차하는 트럭 대수를 최소 2대에서 최대 6대로 변경하면서 시뮬레이션을 수행하였다. Fig. 7은 애니로직의 2차원 가시화 기능을 통해 시뮬레이션 운영 시간에 따른 운반작업 상황을 가시화한 것이다. Fig. 7(a)은 시뮬레이션 운영 시간이 1분일 때의 모습으로, 공차 상태의 첫 번째 트럭이 파쇄장을 출발하여 적재장으로 향하는 모습을 보여주며 나머지 트럭들은 파쇄장에서 대기하고 있다. Fig. 7(b)은 시뮬레이션 운영 시간이 200분일 때의 모습으로, 2곳의 적재장 모두에서 로더가 트럭에 광석을 적재하고 있다. 파쇄장에서는 한 대의 트럭이 파쇄기에 광석을 투하하고 있고, 다른 한 대의 트럭이 파쇄기 이용을 위해 대기하고 있다. 나머지 트럭들은 적재장으로 이동하고 있다. Fig. 7(c)는 시뮬레이션 운영 시간이 300분일 때의 모습으로, 2곳의 적재장 모두에서 한 대의 트럭이 로더를 이용하고 있고 다른 한 대의 트럭은 로더 이용을 위해 대기하고 있다. 파쇄장에서는 트럭이 파쇄기를 이용하고 있으며, 파쇄기를 이용하지 않는 다른 트럭들은 이동하고 있다. Fig. 7(d)는 시뮬레이션 운영 시간이 400분일 때의 모습으로, 적재장 A에서는 트럭이 로더를 이용하고 있으며 다른 트럭은 대기하고 있고 적재장 B에서는 트럭이 로더를 이용하고 있지만, 대기하는 트럭은 없다. 파쇄장에서는 트럭이 파쇄기를 이용하고 있으며, 나머지 트럭들은 이동하고 있다.
Fig. 8은 시뮬레이션 운영 1분 후(a), 100분 후(b), 200분 후(c), 300분 후(d)의 적재장 A, 적재장 B, 파쇄장에서의 트럭의 운반작업 모습을 보여준다.
Fig. 9(a)는 트럭이 시뮬레이션 운영 시간 400분 동안 각 단위 운반작업을 수행한 횟수를 보여준다. 적재장 A에서 78회의 광석 적재 작업이 발생하였으며, 적재장 B에서 77회의 광석 적재 작업이 발생하였다. 파쇄장에서는 148회의 광석 투하 작업이 발생한 것으로 분석되었다. Fig. 9(b)는 시뮬레이션 운영 시간이 300분에서 400분으로 증가할 때 분석된 장비의 평균 이용율, 총 광석 생산량, 현재 단위 시간(분)당 광석 생산량, 하루 평균 수익을 나타낸다. 광석 생산량은 파쇄기에 투하되어 처리되고 있는 광석의 양을 기준으로 산정하였다. 시뮬레이션 결과를 보면, 총 광석 생산량은 약 9,500톤에서 12,500톤으로 증가하였으며, 하루 평균 수익은 약 45,000 USD/day에서 약 68,000 USD/day로 증가하였다.
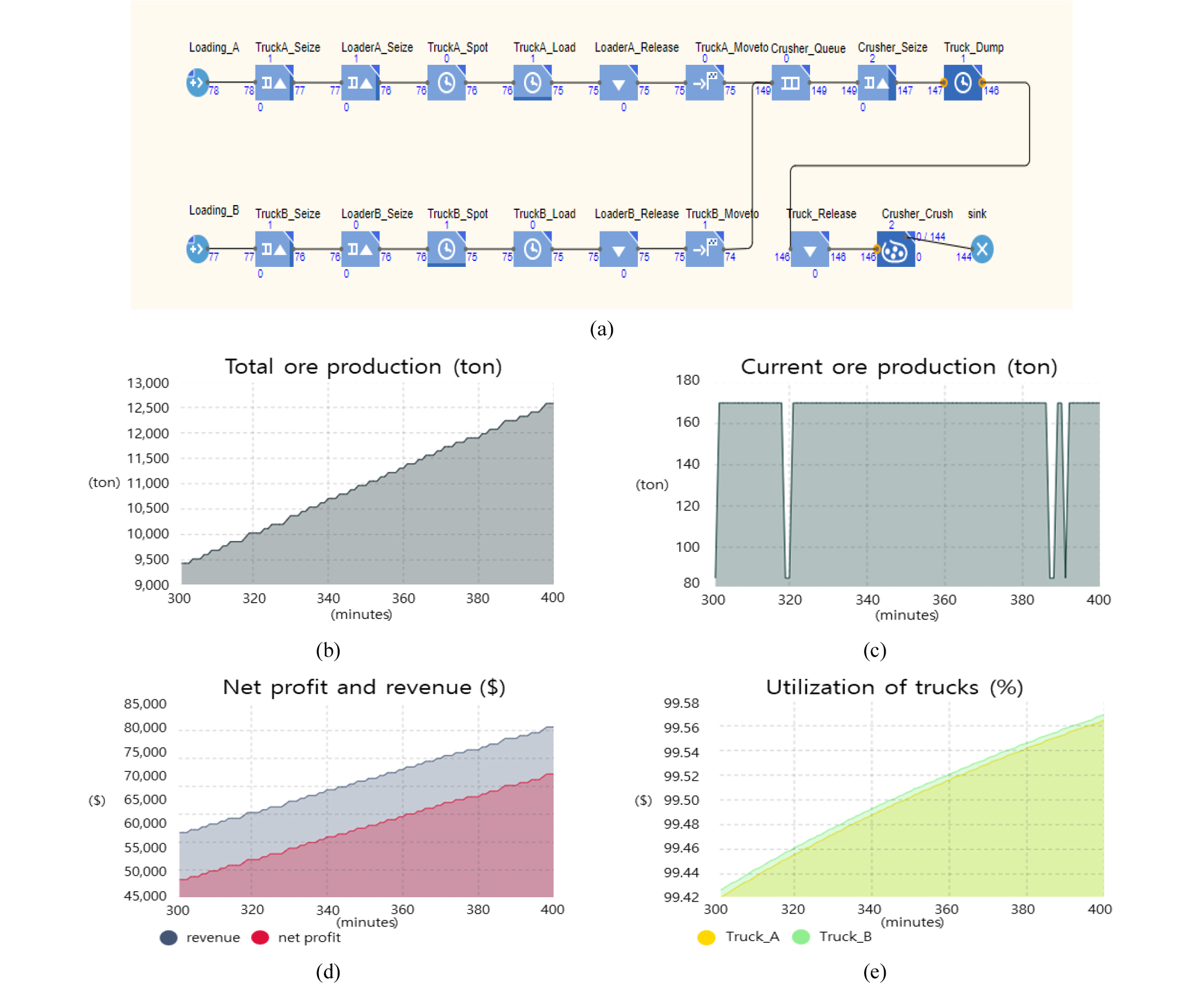
Fig. 9.
Results of truck-loader haulage system simulation during 400 operation times using AnyLogic software. (a) Logic window showing the number of truck operation and operation time during the simulation. (b) Graphical view of simulation results consisting of total ore production (ton/min), current ore production (ton), Net profit and revenue ($) and utilization of trucks (%).
본 연구에서는 시뮬레이션 가시화 결과를 검증하기 위해 연구지역 상공에서 무인 항공기(Unmanned Aerial Vehicle, UAV)를 이용해 작업 일부를 촬영한 동영상과 시뮬레이션 가시화 결과를 비교하였다. Fig. 10은 시뮬레이션 운영 시간을 403분, 405분, 407분으로 설정했을 때 무인 항공기 영상과 시뮬레이션 영상을 비교한 것이다. 실제 작업 영상과 시뮬레이션 가시화 결과가 유사한 것으로 보아 애니로직을 통해 개발한 시뮬레이션 알고리즘이 연구지역 현장의 운반시스템을 잘 반영하고 있음을 확인할 수 있었다.
Table 2는 적재장 A와 적재장 B에 배차된 트럭 대수 조합을 달리 설정했을 때 분석된 시뮬레이션 결과를 보여준다. 신기 사업소 5지구에서는 트럭을 적재장 A에 4대를 배차하고 적재장 B에 4대를 배차할 때 하루 평균 수익이 69,252 USD/day로 가장 높게 나타났고, 이때의 총 광석 생산량도 12,920 ton으로 가장 많게 분석되었다.
Table 2. Comparison of simulation results according to the number of trucks dispatched to loading area A and area B
8대의 트럭을 적재장 A와 적재장 B에 배차할 때, 두 적재장에 배차된 트럭의 대수 차이가 증가할수록 총 광석 생산량과 파쇄장에서의 트럭 대기시간은 점차 감소하는 것으로 분석되었다. 적재장 A에 많은 수의 트럭을 배차할 경우 적재장 A에서의 트럭 대기시간은 증가하고 적재장 B에서의 트럭 대기시간은 감소하였다. 이에 따라 적재장 A에 배차된 트럭들의 광석 운반 횟수는 감소하여 총 광석 생산량은 감소한 것을 볼 수 있다. 또한, 적재장 A에 배차된 트럭들이 파쇄장을 방문하는 횟수가 감소하여 파쇄장에서의 트럭 대기시간도 감소하였다. 만약 두 적재장에 동일한 대수의 트럭을 배차할 경우, 두 적재장 모두에서 광석 적재 작업이 균형 있게 이루어져 두 적재장에 배차된 트럭들이 파쇄장을 동시에 방문할 확률이 높아진다. 따라서 이 경우에는 파쇄장에서의 트럭 대기시간이 크게 길어질 수 있다.
토 의
노천광산의 트럭-로더 운반시스템을 효과적으로 운영하기 위해서는 시스템에 투입되는 트럭의 수, 파쇄기의 처리 속도를 최적화할 필요가 있다. 시뮬레이션 운영 조건을 앞선 연구와 동일하게 설정하고 트럭의 수와 파쇄기의 처리 속도를 달리 설정하여 시뮬레이션을 수행하였다. Table 3은 파쇄기 처리 속도를 달리 설정했을 때 변화하는 시뮬레이션 결과 지표 값을 보여준다. 신기 사업소 5지구에서 보유하고 있는 8대의 트럭을 기준으로 적재장 A에 4대의 트럭을 배차하고 적재장 B에 4대의 트럭을 배차한다고 가정했을 때, 파쇄기 처리 속도를 1,000 ton/hour에서 1,800 ton/ hour까지 100 ton/hour 씩 증가시켰다. 그 결과 파쇄기의 처리속도가 1,700 ton/hour일 때 하루 평균 수익이 77,428 USD/day로 가장 높게 분석되었으며, 이때의 트럭 A의 이용율은 약 86.84%, 트럭 B의 이용율은 약 87.01%로 나타났다. 반면에, 처리 속도가 1,800 ton/hour 일 때 분석된 하루 평균 수익은 76,406 USD/day로 처리 속도가 1,700 ton/hour일 때보다 더 낮게 나타났다. 파쇄장에서의 대기시간이 증가함에 따라 트럭 순환 시간이 지연되었기 때문에 파쇄기의 처리 속도가 빨라져도 하루 평균 수익이 증가하지 않은 것으로 판단된다.
Table 3. Comparison of simulation results according to capacity of crusher
Table 4는 트럭의 수를 9대와 10대로 증가시킨다고 가정했을 때 분석된 시뮬레이션 결과 지표 값을 나타낸다. 총 트럭의 대수가 9대일 때는 각 적재장에 최소 2대부터 최대 7대까지 차례대로 배차하였고, 총 트럭의 대수가 10대일 때는 각 적재장에 최소 2대부터 최대 8대까지 차례대로 배차하여 시뮬레이션을 수행하였다. 그 결과 트럭이 총 9대일 때는 적재장 A에 4대의 트럭을 배차하고 적재장 B에 5대의 트럭을 배차할 때 하루 평균 수익이 68,047 USD/day로 가장 높게 나타났다. 트럭이 총 10대일 때는 적재장 A에 4대의 트럭을 배차하고 적재장 B에 6대의 트럭을 배차했을 때 하루 평균 수익이 67,864 USD/day로 가장 높게 분석되었다. 그러나 두 경우 모두 8대의 트럭을 배차했을 때 분석된 최대 수익이 69,252 USD/day를 초과하지 못하였다. 이는 파쇄기 처리 속도가 1,000 ton/hour로 고정되었기 때문에 트럭의 수가 증가하여도 하루 평균 수익이 증가하지 않은 것으로 판단된다.
Table 4. Comparison of simulation results considering additional truck dispatch
결 론
본 연구에서는 애니로직을 이용하여 노천광산 트럭-로더 운반시스템 시뮬레이션의 작업 상황을 실시간으로 가시화하고, 시간에 따라 변화하는 광산의 주요 생산지표들을 확인할 방법을 제시하였다. 국내 석회석 노천광산을 대상으로 이 방법을 적용한 결과 시간의 흐름에 따라 트럭-로더 운반시스템에 나타나는 사건들을 실시간으로 가시화할 수 있었다. 또한, 실시간으로 변화하는 시뮬레이션 결과 지표 값을 확인할 수 없었던 기존 프로그램들의 한계를 극복할 수 있었다. 연구지역에 대한 트럭-로더 운반시스템 시뮬레이션 알고리즘을 설계하여 하루 작업 시간(480분) 동안의 시뮬레이션을 수행한 결과, 적재장 A에 4대의 트럭을 배차하고 적재장 B에 4대의 트럭을 배차하여 시스템을 운영하는 것이 경제적인 측면에서 가장 효과적인 것으로 분석되었다.
본 연구에서는 시뮬레이션 결과의 가시화 과정에서 배경에 해당하는 노천광산의 영상은 2차원 자료를 사용하였다. 노천광산의 실감형 디지털 트윈 구축 등 보다 고도화된 시뮬레이터 개발을 위해서는 무인항공시스템을 이용해서 생성한 노천광산의 고정밀 3차원 모델링 자료를 시뮬레이션과 결합하기 위한 추가적인 연구가 필요하다고 판단된다.