서 론
디지털 트윈의 개요
자원공학 분야에서의 디지털 트윈 적용 사례
Haile Gold Mine (USA)
Ban Houayxai Gold-Silver Mine (Laos)
Imsa Well (Norway)
전망 및 과제
결 론
서 론
ICT(Information and Communication Technology)기술이 발달하면서 스마트 광산, 디지털 오일필드를 비롯한 정보통신 기술의 자원공학 분야 도입이 가속화되고 있다(Lim et al., 2014; Choi, 2017). 특히 최근에는 빅데이터, 인공지능과 같은 4차 산업혁명 관련 기술들이 부각되면서 자원 개발의 효율화와 안전성 제고를 위한 관련 응용기술들의 개발이 활발하게 이루어지고 있다(Choi, 2018). 디지털 트윈(Digital Twin, DT)은 이러한 첨단 정보통신 기술들 중에서도 핵심 중 하나로 평가되는 것으로서, 단순하게 표현하면 현실의 어떤 대상을 가상 세계에 그대로 복제한 것을 말한다. 여기서 복제라는 것은 현장 조사를 통해 데이터를 취득하는 정도가 아니라, 현실 세계의 대상에서 어떠한 값의 변화가 일어났을 때 이것을 실시간에 가깝게 복제하고 그 대상이 변화하는 양상까지 모사함으로써 현실 세계의 일부를 가상으로 구현하는 것을 목표로 한다(Tao et al., 2018). 이와 같이 구현된 디지털 트윈은 복잡한 현실의 객체 특성이나 변화를 반영하게 되므로 대상의 현재 상태를 진단하거나 미래를 예측하기 위한 도구로 활용될 수 있다. 예를 들어 어떠한 광산 내에 운용 중인 모든 운반 트럭의 오일 상태, 각종 소모품의 마모도와 오염도, 주요 동력 전달 부품들의 상태와 같은 모든 중요 정보를 항상 실시간으로 알 수 있다면, 각 부품에 대한 수리나 교체 시기를 미리 예상함으로써 불필요한 점검이나 지나치게 늦은 수리로 인한 시간적, 비용적, 인적 효율성 저하가 크게 줄어들 것이다.
본래 디지털 트윈은 제조업에서의 제품수명주기관리(Product Lifecycle Management, PLM)를 목적으로 제시된 개념으로서, 제품의 설계, 제조 및 활용 단계에서의 각종 시뮬레이션, 이력 추적, 실시간 대응과 예측을 위하여 도입되었다(Grieves, 2019). 이와 같은 특징은 실물을 가공, 생산한다는 점과 이를 위한 지속적인 예측 및 대응이 요구된다는 점에서 자원공학 분야에서도 동일한 관점에서 유효하게 활용될 수 있다. 또한 디지털 트윈은 그 자체로서 현실 세계의 물리적 속성과 변화 과정을 대변하므로, 매번 직접 수행하기 어렵거나 많은 인적, 시간적, 물적 자원이 소모되는 일련의 계획에 대한 수립, 실행과 변경에 적합하다. 이렇듯 자원 생산 효율성의 증대와 자동화를 동반한다는 점에서 디지털 트윈은 운영 비용 상승, 인력 충원 문제, 노령화 등의 어려움을 겪고 있는 국내 광업계를 활성화하기 위한 기술로서 고려될 필요가 있다(Choi, 2017).
디지털 트윈은 아직 완전히 정립된 분야가 아니며, 그 정의와 사용 목적 또한 많은 기관과 연구자들에 의해 조금씩 다르게 기술되어 왔다(Schleich et al., 2017; Kritzinger et al., 2018). 그럼에도 불구하고 2019년까지 디지털 트윈을 이미 도입한 기업체가 13%, 1년 내에 도입을 시작할 것으로 조사된 기업체가 62%에 달하며, 이러한 추세에 따라 Gartner에서는 디지털 트윈을 2019년 10대 전략 기술 트렌드 중 하나로서 선정하였다(Gartner, 2019; Cearley and Burke, 2019). 또한 IDC(International Data Corporation)의 보고서에 의하면 2024년까지 25%의 광업 회사가 디지털 트윈을 도입할 것으로 예측되었으므로 현재는 분야와 무관하게 디지털 트윈의 본격적인 활용을 앞두고 있는 시기로 볼 수 있다(Ditton et al., 2018). 본 논문에서는 이와 같은 점에 주목하여 디지털 트윈의 기본적인 개념과 이를 자원공학 분야에서 활용한 사례를 살펴봄으로써 향후 전망에 대하여 논의해 보고자 한다.
디지털 트윈의 개요
디지털 트윈의 여러 정의 중 가장 일반적으로 통용되는 것은 Glaessgen과 Stargel(2012)에 의해 제시된 ‘복합적인 제품의 수명을 반영하기 위해 물리 모델, 센서 등을 활용하는 다중 물리, 다중 규모, 확률적 통합 시뮬레이션’이다. 이를 일반적으로 풀이하면 모델과 데이터를 통해 현실의 객체가 갖는 속성과 거동을 동일하게 반영할 수 있는 종합적인 시뮬레이션 체계라고 할 수 있다(Haag and Anderl, 2018).
이상적인 관점에서는 현실 세계의 어떠한 부분에 대한 디지털 트윈을 보유한다는 것이 곧 해당 지점의 특성을 알기 위해 해당 지점에 직접 방문하여 살펴보는 것과 가상 공간상에서 그 지점의 디지털 트윈을 살펴보는 것에 차이가 없거나, 심지어 후자가 더 나은 수준을 의미한다(Grieves, 2019). 그러나 현실의 대상에 대한 모든 정보를 실시간으로 전부 복제하는 것은 불가능하며, 그것이 가능하다 하더라도 비효율적이므로 디지털 트윈의 구현을 위해서는 그 목적과 얻어야 하는 인자들의 중요도에 따라 데이터와 모델의 수준 및 자료의 획득 방법을 결정할 필요가 있다(Cameron et al., 2018).
디지털 트윈을 구성하는 데이터는 비휘발성(nonvolatile) 데이터와 휘발성(volatile) 데이터로 구분할 수 있다. 전자는 시간의 흐름에 크게 영향 받지 않는 시설의 형상과 규격, 배치 등에 관련된 것이므로 측정과 조사 등을 통해 획득될 수 있다. 반면 후자는 물질의 유동이나 온도 변화 등과 같이 시간에 따른 변화가 큰 것으로서 자동화된 계측이 반드시 필요하다(Uhlemann et al., 2017a, Uhlemann et al., 2017b).
이처럼 현실로부터 복제되는 실시간적 정보를 갖는다는 특성에 의해 디지털 트윈은 기존의 센서를 동반한 데이터 수집 체계나, 이를 응용한 사물인터넷(Internet of Things, IoT) 또는 가상물리시스템(Cyber-Physical Systems, CPS)과 기술적으로 유사하면서도 깊은 연관성을 갖는다. 특히 가상물리시스템은 디지털 트윈과 마찬가지로 현실과 가상의 융합 체계로서 제안되었으며, 현실의 센서들로부터 대상의 물성을 취득하여 이를 분석하고 그 결과를 대상의 운영이나 조작에 반영하는 일종의 피드백 구조를 가진다는 점에서 유사하다(Tao et al., 2019). 앞선 기술들과 비교하여 디지털 트윈이 갖는 가장 큰 특징은 디지털 트윈 자체가 현실의 대상을 대변할 수 있을 정도로 시간적, 구조적 동일성을 지닌다는 점과, 복제된 현실의 대상을 가상의 환경에서 지속적으로 시뮬레이션함으로써 현실과 동일한 시점이나 미래의 가상적 복제체를 생성할 수 있다는 점에 있다(Suh and Ji, 2019).
Fig. 1은 단위 시간의 흐름에 따른 디지털 트윈의 구성 및 활용 양상을 예시한 것이다. 현실 세계의 대상(Fig. 1a)이 갖는 각종 형태와 물성들은 취합, 변환되어 구조화된 데이터의 형태를 갖는 복제체(Fig. 1b)로 구성된다. 이때 현실의 대상이 갖는 정보를 실시간으로 복제하기 위해 센서나 RFID(Radio-frequency identification) 태그와 같은 장비로부터 정량적인 자료를 취득하는 단계가 포함되며(Fig. 1c), 이는 사물인터넷으로 대표되는 센서 네트워크 등의 기반 기술과 장비들로 획득된다. 이렇게 생성된 복제체는 아주 짧은 시간의 현실을 대변하게 되므로 복제를 포함한 전체 과정은 지속적으로 반복 수행되어야 한다(Renzi et al., 2017). 해당 복제체는 그 자체로서도 현실의 다양한 인자와 물성을 구조적으로 포함하는 데이터로서의 가치를 가지며, 현실과 달리 시간이 지남에 따라 누적되므로 이를 이용한 학습이나 분석에 사용될 수 있다.
복제체는 현실에서 수행하는 것(Fig. 1d)과 동일한 거동을 모사하거나 예측할 수 있는 가상의 운영 또는 시뮬레이션(Fig. 1e)을 거침으로써 또 다른 복제체를 생성할 수 있다. 이 복제체는 시뮬레이션의 시간적 주기 또는 반복 횟수 등에 따라 (1)다음 복제체가 생성되는 근미래 시점(Fig. 1f) 또는 (2)그보다 먼 미래의 시점(Fig. 1g)을 대변한다. 여기서 시뮬레이션은 인공지능을 통해 학습되었거나 물리적, 통계적 방법 등으로 정의된 일련의 모델을 통해 예측되는 다음 복제체를 생성하는 것으로서 그 대상과 방법은 목적에 따라 매우 다양하다(Negri et al., 2017). (1)의 경우는 높은 확률로 현재의 시점을 대변하는 가상의 복제체를 생성하는 것이므로 이상에 대한 동시적 대응이나 시뮬레이션에 기반한 가상 센서(virtual sensor)의 용도로서 활용될 수 있다(Renzi et al., 2017). (2)는 (1)과 동일하거나 유사한 방법으로 미래를 예측하는 것으로서 지속적으로 변화하는 현실 정보에 기반한 중장기적 예측을 수행하게 되므로, 시설이나 장비의 노후화나 고장 시점 등을 미리 예측하여 이에 대비하는 예지 보전(predictive maintenance)에 활용된다(Glaessgen and Stargel, 2012). 또한 Fig. 1e와 같은 가상의 시뮬레이션에 입력되는 모든 인자가 반드시 이전 시간의 실제 데이터일 필요는 없으므로, 이러한 점을 이용하면 기반 시설의 구축이나 작업 공정의 변경을 현재 시점의 운영 변수를 포함하여 시험해 봄으로써 잠재적 위험을 줄이면서도 비용적인 효율을 제고할 수 있다(Rossi, 2017).
자원공학 분야에서의 디지털 트윈 적용 사례
Haile Gold Mine (USA)
Haile 광산은 사우스캐롤라이나 주에 위치한 노천 금광으로서 1827년부터 채광을 개시하였으며, 파분쇄, 선광 및 습식 제련시설을 통해 연 3,345 kg의 금을 생산하고 있다(Schug et al., 2019). 해당 광산에서는 습식 사이클론으로 공급되거나 농축조(thickener)에서 배출되는 슬러리에 대한 밀도 측정 센서가 부정확하면서도 잦은 보정이 필요한 점 등의 문제점이 있었으며, 이를 해결하기 위한 방안으로서 디지털 트윈을 활용하고자 하였다. 해당 광산에서는 제련시설의 자동화 및 무인화를 목표로 하는 가상 시뮬레이션 모델과 제어 시스템을 사전에 도입하여 운영하고 있었으며, 이러한 시스템에 실시간 데이터 수집 및 처리 모델을 결합하여 단일 체계화함으로써 디지털 트윈을 구축하였다. 이를 위하여 Table 1과 같은 입력 인자를 설정하여 센서를 배치하고, 해당 데이터를 시뮬레이션 모델과 연동하였다.
Table 1. Parameters for digital twinning of Haile gold mine (Schug et al., 2019)
시뮬레이션 모델은 앞선 인자들을 종합하여 특정 위치의 이론적인 물성값을 계산하고 이를 센서 측정값과 비교하는 작업을 수행한다. 일례로서 습식 사이클론의 슬러리 밀도에 대한 실시간 시뮬레이션 수치의 평균 제곱근 편차(RMSD, root mean square deviation)는 약 2%로서 이를 벗어난 수치를 보일 경우 센서에 대한 이상으로 간주하여 관리자에게 보고된다. 이외에도 위치별 값의 변동과 분석을 통해 펌프 및 파이프의 손상, 센서의 보정 필요성 감지와 같은 설비별 비정상적 가동을 감지하는 모니터링이 수행되고 있다(Moore, 2018).
Ban Houayxai Gold-Silver Mine (Laos)
해당 광산은 라오스에 위치한 노천광산으로서 2012년부터 금, 은의 생산을 시작하였으며, 이 광산에서는 MAXTATM 솔루션을 통해 디지털 트윈을 해당 현장에 적용하였다(Petra Data Science, 2019). 디지털 트윈은 금속의 회수율을 제고하는 것과 천공, 발파 시 암종 등에 따른 최적화를 실시하여 분쇄 효율을 높이기 위한 목적으로 적용되었다. 이를 위하여 2016년부터 2018년까지 2년간 채굴된 약 1천만 톤의 광석에 대한 데이터를 인공지능으로 학습하였으며, 이를 실시간 데이터와 연동하여 회수율이 높을 것으로 추정되는 지점을 파악하거나 향후 예측되는 분쇄기의 시간당 처리량을 출력하고, Fig. 2와 같이 현재 시행 중인 발파작업의 최소저항선, 공간격, 지름 등의 인자들을 변경하여 그에 따른 예상 출력량을 시뮬레이션할 수 있다(Carpenter et al., 2018).
Imsa Well (Norway)
eDrilling은 노르웨이에 위치한 시추 관련 솔루션 기업으로, 시뮬레이터를 기반으로 하는 시추 제어 및 최적화, 가시화 등에 대한 디지털 트윈 기술을 적용하고 있다. 해당 기술은 기존에 개발된 수학적 모델과 모니터링, 가시화 등을 포함하는 실시간 시뮬레이터 및 모델을 디지털 트윈으로 재정의한 것이며, 대표적으로 노르웨이의 Imsa 유정에 적용되었다(Mayani et al., 2018).
본 사례에서는 유정의 물리 모델을 온도와 유압 등을 포함하는 수리 모델과 토크, 항력 등을 계산하기 위한 역학 모델로 나누어 구성하고, 이 모델을 통해 WOB(Weight On Bit), TOB(Torque On Bit), 장력, 회전량, 변위 등을 계산한다. 이와 함께 이수의 밀도와 압력, 온도, 유체의 흐름, 유정 제어, 토크, 항력 등에 대한 실시간 시뮬레이션을 수행하며, SPP(Stand Pipe Pressure) 등의 계산값을 센서를 통해 측정된 실제 수치와 함께 표출하여 특정 부분에 대한 이상이 발생하였는지를 감시할 수 있다(Fig. 3). 또한 현재까지의 운영 데이터를 기반으로 한 사전 시뮬레이션을 통해 향후 12~24시간동안의 거동을 예측함으로써 시추 작업의 최적화 및 위험 요소의 제어에 활용하고 있다(Scott et al., 2016; Nabavi et al., 2016).
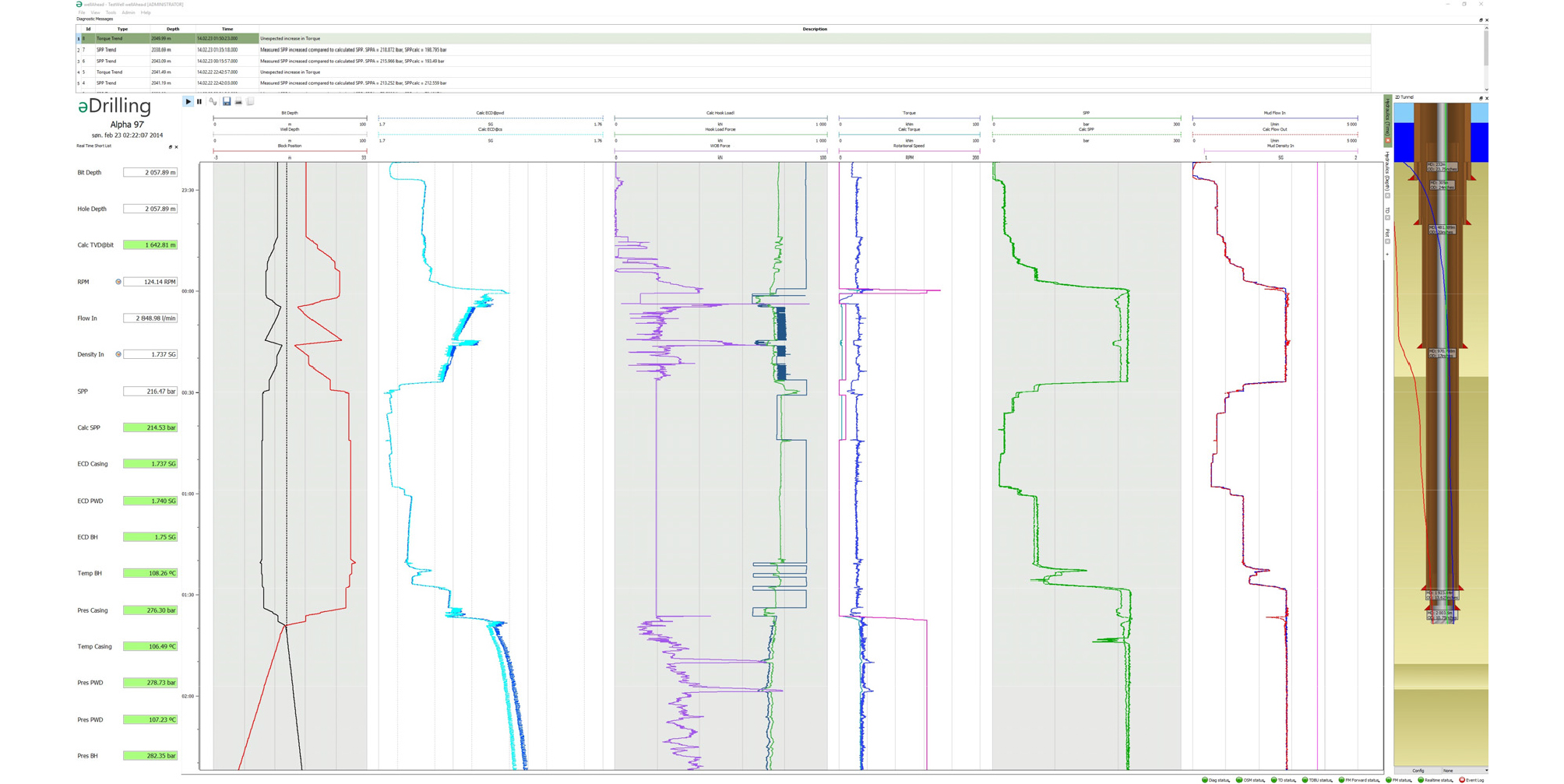
Fig. 3.
eDrilling’s DT-based visualization and dynamic performance optimization for drilling operations (eDrilling, 2019).
전망 및 과제
EY(Ernst & Young)에서는 2019년 발간한 보고서에서 광업에서의 디지털 트윈에 대하여 다음과 같은 세부 분야들을 제시하였으며, 이는 개괄적 예시로서 모든 자원공학 분야에 유사하게 적용될 수 있다(EY, 2019).
(1) 광산 운영: 광산 내 장비 유지보수 및 유휴 시간의 최적화를 통한 예측적인 관리
(2) 자원 처리: 예측 정비 기반 설비 관리 및 실시간 데이터 기반 공정 제어 인자의 최적화를 통한 생산성 향상
(3) 운송: 운송망 최적화 및 관리를 이용한 운송 신뢰성 향상
(4) 종단간 생산성 최적화: 전체 생산 단계에서의 시나리오별 시뮬레이션과 분석을 통한 최적의 계획 수립
앞서 살펴본 적용 사례들은 장비나 시설의 관리 및 운영에 대한 최적화에 해당하는 (1)~(2)에 집중되어 있으며 그 대상들도 고정된 장비에 국한되므로, 이것은 현재 자원공학 분야에서도 타 분야와 마찬가지로 디지털 트윈의 도입 초기 단계에 있음을 시사한다. 디지털 트윈은 아직 표준적인 기술 정의나 프레임워크 등이 개발되지 않은 상태이므로, 탐사에서 생산 및 운영 등의 모든 단계에서 특정 솔루션을 통해 디지털 트윈을 도입하는 것은 부적합하다. 그러나 디지털 트윈의 정의 및 활용 구조를 종합하였을 때 이는 다른 4차 산업 관련 기술들과 마찬가지로 완전히 새로운 기술이라고 하기는 어려우며, 특히 공학적인 관점에서는 온라인 네트워크를 통해 조직화, 고속화 및 자동화된 시뮬레이션 체계에 가깝다고도 볼 수 있다(Soderberg et al., 2017; Cameron et al., 2018). 체계화된 데이터와 모델을 통한 시뮬레이션은 자원공학 분야에서 장기간 수행되어 왔으므로, 앞선 적용 사례들과 같이 기존의 시뮬레이션 체계와 결합하여 운영의 최적화나 제어, 예측 등의 새로운 기능성을 창출한다면 새로운 기술의 개발이 아닌 선행 기술의 발전 단계로서 원활한 개발을 기대할 수 있다.
또한 디지털 트윈의 최종적인 구축은 거시적인 수준에서 다수의 장비, 시설과 인력 등에 대한 종합적인 시뮬레이션 체계를 구축하는 것이지만 이를 단일 수준에서 일괄적으로 구축하기 위해서는 그 복잡도가 지나치게 상승한다(Martinez et al., 2018). 다양한 분야에서 디지털 트윈 관련 솔루션을 제공하고 있는 Simens에서는 디지털 트윈을 먼저 시설과 모델로 구분하고, 이를 다시 개별 장비와 이들이 모인 단위 시스템, 그리고 이 시스템이 다시 결합된 전체 시설로 구분하여 각 요소 단위별 데이터와 모델이 각 수준에 적합하게 서로 결합되어 종합적인 체계를 구축하는 방식을 사용하였다(Grange, 2018; Zborowski, 2018). 디지털 트윈의 도입이 시작되는 현 상황에서는 이와 같이 개별 단위에 대한 구축이 우선적으로 도입되는 것이 합리적이므로 각 부분별 시뮬레이션이 구조적으로 통합되는 형태의 단계적 도입이 현실적인 방안으로 판단된다.
디지털 트윈의 도입과 관련하여 제시된 또 다른 문제들로서는 (1)기존의 분산된 비표준적, 수동적 데이터 취득 과정, (2)높은 IT환경의 도입 비용, (3)데이터 보안 문제, (4)불완전한 시뮬레이션과 최적화 기술의 결합 문제 등이 있다(Uhlemann et al., 2017a). 이 중 (1)~(3)은 디지털 트윈뿐만 아니라 전반적인 ICT(Information and Communication Technology) 관련 기술들의 도입에 적용되는 것이나, 디지털 트윈의 경우 데이터의 자동화된 취득과 시뮬레이션, 이를 통한 제어 등의 전반적인 운영 프로세스에 적용되어야 하므로 해당 문제들이 일종의 선결 사항으로 작용한다. 이를 해결하기 위해서는 IoT를 위시한 기반 기술들의 도입이 단계적으로 선행되어야 하며(Kritzinger et al., 2018), 초기 구축 및 운영비용을 회수하면서도 추가적인 이득을 얻기 위해서는 기술의 도입을 통해 시설, 장비 및 전체 운영의 최적화 수준을 지속적으로 제고하면서도 일정 이상의 운영 기간이 필요할 것이다. 이러한 점에 있어 자원공학 분야는 탐사, 개발, 생산, 처리 등의 복잡한 운영 과정들이 다수의 높은 운영비용을 동반하는 시설물 및 장비를 통해 장기간 이루어지므로 기술 도입을 통한 자동화와 효율화를 통한 이익을 기대할 수 있다.
(4)는 시뮬레이션의 시간적 효용성과 관련된 문제로서, 다중 시뮬레이션을 통한 운영 인자의 지속적인 최적화와 예측을 수행하기 위해서는 시뮬레이션의 실시간성이 확보되어야 한다. 따라서 클라우드 컴퓨팅을 비롯한 빅데이터 관련 연산기술들과 함께 데이터 기반 및 시뮬레이션 기반 모델의 결합을 통해 디지털 트윈 모델의 고속화가 필요하며, 이와 같은 전반적인 데이터 처리 및 모델링을 위해서는 다학제적인 연구 및 개발이 필수적으로 요구된다(Cameron et al., 2018).
결 론
디지털 트윈은 현실의 구성요소들에 대한 형상과 물성을 실시간으로 반영하는 데이터와 이를 구동하는 모델을 활용한 시뮬레이션을 통해 현실을 모사, 예측함으로써 이상 대응, 예방 정비, 운영 인자의 최적화 등에 활용할 수 있다. 이러한 점을 기반으로 현재 다양한 분야에서 도입을 시작하는 단계에 와 있으며, 자원공학 분야에서는 채광, 선광, 시추 등의 일부 사례를 통해 향후 활용 가능한 양상을 살펴볼 수 있다. 현재는 주로 일부 장비나 운영 단계의 최적화와 예측 등에 국한되어 활용되고 있으나, 통신 네트워크로 연결되어 있다는 점과 현실의 거동을 반영하는 점을 응용하면 가상현실을 통한 원격 운영이나 교육, 작업자 안전 등의 응용 기술들로 확장이 가능하다. 이러한 특성을 활용한다면 향후 다양한 ICT기술들과의 복합적인 활용이 가능할 것이며, 이를 통해 무인화, 자동화, 효율화 등의 직접적인 이득뿐 아니라 국내 자원 개발의 활성화를 통한 국가적 이익에도 기여할 수 있을 것으로 기대된다.