서 론
유화산 산처리 공법 기술 특성
유화산의 제조 및 안정성 평가
유화산 제조
안정성 평가
유화산 산처리 공법 메커니즘
현장 적용사례 분석
Sungai Kenawang 가스전
BMB 유전
Mumbai High 유전
결 론
서 론
탄산염암 저류층에는 전 세계 오일의 60% 이상이 부존된 것으로 알려져 있지만 공극률과 투과도의 불균질성(heterogeneity)이 크고 2차 공극구조(secondary porosity)의 발달로 인해 유동 특성이 복잡하다(Schlumberger, 2020). 따라서 개발과 생산이 쉬운 사암 저류층보다 1차 회수율이 현저히 낮게 나타나며, 석유개발 현장에서는 이러한 탄산염암 저류층의 투과도를 개선하고 생산성을 증진하기 위해 암체 산처리 공법(matrix acidizing)을 주로 수행한다(Yousufi et al., 2018; Sidaoui et al., 2018; Jafarpour et al., 2019). 암체 산처리 공법은 Fig. 1과 같이 지층의 파쇄압(fracture pressure)보다 낮은 압력으로 저류층에 산(acid)을 주입하여 유정 주변의 손상된 영역을 개선하고 웜홀(wormhole)이라 불리는 고투과성 통로를 형성하는 유정자극법(well stimulation) 중 하나이다(Lund et al., 1973; Sokhanvarian et al., 2019). 이때, 암체의 파쇄를 피하기 위해서는 저류층에 주입하는 유체의 주입률(injection rate)을 낮게 유지하는 것이 중요하다(Zakaria and Nasr-El-Din, 2016).
염산(HCl)은 가격이 저렴하고 방해석(calcite)과 백운석(dolomite)으로 이루어진 탄산염암과의 반응성이 좋아 암체 산처리 공법에 널리 사용된다. 하지만 염산은 점성도가 낮아 저류층에 주입 시 투과도가 높은 지층으로만 흐르게 되어 부분적인 산처리를 하게 되고 저류층의 전체적인 투과도를 개선하기 어려운 단점이 있다(Nasr-El-Din et al., 1999; Daeffler et al., 2018). 또한, Fig. 2와 같이 낮은 주입률에서는 염산의 강한 반응성 때문에 암석의 주입부만 암석이 용해되는 표면용해(face dissolution) 현상이 일어나게 되며, 고온에서는 생산설비에 대한 부식성이 매우 높아 이를 보호하기 위해 고가의 부식방지제(corrosion inhibitor)를 대량으로 사용해야 하는 문제가 있다(Sayed and Nasr- El-Din, 2013; Carins et al., 2016; Sidaoui et al., 2018).
염산을 이용한 기존의 암체 산처리 공법의 한계점을 보완하기 위해 산의 점성도를 높여 체적접촉효율(volumetric sweep efficiency)을 개선하고 산과 암석의 반응을 지연시켜 효율적인 웜홀을 형성하는 산 혼화(acid divergent) 기법들이 연구되어 왔다(Nasr-El-Din et al., 2001; Carins et al., 2016). 폴리머(polymer)를 기반으로 한 겔화산(gelled acid)은 산의 점성도를 증가시켜 산과 암체의 체적접촉효율을 높이고 투과도가 상이한 저류층에 골고루 웜홀을 생성하여 산처리 공법의 효율을 높인다(Zakaria and Nasr-El-Din, 2016). 하지만 겔화산은 치밀한 탄산염암(tight carbonate) 저류층에 주입 시 염산과 폴리머가 분리되며, Fig. 3의 (a)와 같이 암석 주입부의 투과도를 낮추는 폴리머 필터-케익(filter-cake)을 형성함으로 공법이 실패하는 문제점이 있다(Gomaa and Nasr-El-Din, 2010; Zakaria and Nasr-El- Din, 2016). 또한, 불완전한 폴리머 중합(polymerization)으로 인해 염산에 완전히 용해되지 않은 폴리머가 Fig. 3의 (b)와 같이 젤라틴(gelatin) 형태로 뭉쳐져 저류층에 유체의 주입이 불가능하게 된다(Mark and Kroschwitz, 1985; Wang et al.,2020).
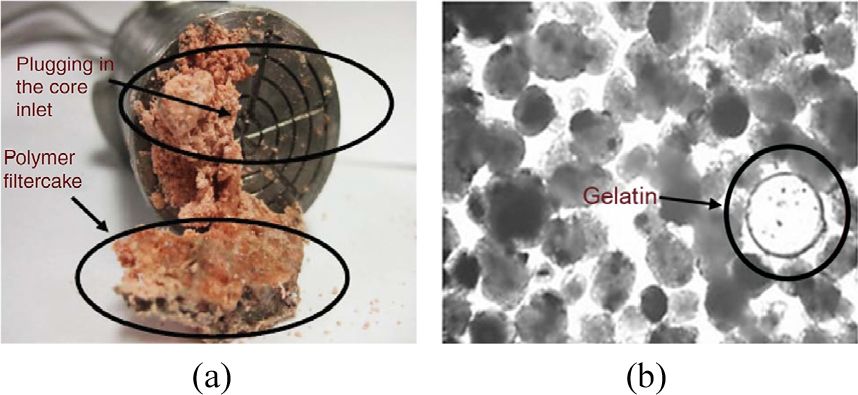
Fig. 3.
Limitations of polymer-based acid, (a) Polymer filter-cake at core inlet part (Zakaria and Nasr-El-Din, 2016), (b) Inhomogeneous polymerization problem (Mark and Kroschwitz, 1985).
유화산(emulsified acid)은 염산에 오일과 유화제(emulsifier)를 함께 혼합하여 산의 점성도를 증가시킨 것으로 저류층에 유체의 주입압력을 낮게 유지한다. 특히, 유화산 내의 오일이 산과 암석의 반응을 지연시키는 장점이 있으며, 생산설비의 부식을 방지하기도 한다(Kasza et al., 2006; Madyanova et al., 2012; Sarma et al., 2012). 이러한 특징으로 인해 중동지역의 탄산염암 저류층에서 유화산 산처리 공법에 대한 관심이 계속 증가하고 있으나 아직 국내에서는 이에 대한 연구가 전무한 상황이다(Sidaoui and Sultan, 2016). 따라서 본 연구에서는 탄산염암 저류층에서 유화산 산처리 공법의 기술 특성 및 메커니즘을 조사하고 현장사례를 분석함으로써 향후 유화산 산처리 공법을 적용한 유정의 생산성 개선 프로젝트 설계를 위한 기초자료를 제시하고자 한다.
유화산 산처리 공법 기술 특성
에멀젼(emulsion)은 Fig. 4와 같이 수상(water phase)이 연속상(continuous phase)을 이루는 O/W(oil-in-water) 에멀젼과 유상(oil phase)이 연속상을 이루는 W/O (water-in-oil) 에멀젼으로 나뉜다(Sidaoui and Sultan, 2016). 탄산염암 저류층의 암체 산처리 공법에서 사용하는 유화산은 염산이 오일 내에 액적(droplet)으로 분산되어 있는 W/O 에멀젼으로, 이때 사용하는 오일은 염산과 탄산염암이 빠르게 반응하는 것을 막는 확산장벽(diffusion barrier) 역할을 한다(Al-Anazi et al., 1998; Sayed and Nasr-El-Din, 2013; Carins et al., 2016; Sokhanvarian et al., 2019). 유화산의 확산장벽으로 인해 산과 암석의 반응 속도가 지연되어 저류층 내에 깊은 웜홀을 생성할 수 있게 되며, 염산이 생산 설비와 직접 접촉하지 않아 설비의 부식이 최소화되어 부식방지제의 첨가를 최소화 할 수 있다(Sidaoui and Sultan, 2016). 유화제는 친수성(hydrophilic)인 머리(head)와 친유성(hydrophobic)인 꼬리(tail)로 구성되어 있으며, 수상인 염산과 유상인 오일 사이의 계면에 흡착하여 계면장력(interfacial tension)을 낮추고 유화산을 형성하게 하는 중요한 첨가제이다(Fig. 4).
친수성-친유성 밸런스(hydrophile-lipophile balance, HLB) 값은 유화제의 친수성 및 친유성 정도를 나타내는 특성으로, 0에 가까울수록 친유성, 20에 가까울수록 친수성을 띈다. 이를 통해 유화산의 형태(W/O emulsion, O/W emulsion)를 결정되므로 W/O 유화산을 제조하기 위해서는 HLB 값을 고려하여 알맞은 유화제를 선택하여야 한다. Table 1은 HLB 값 범위에 따른 대표적인 유화제의 종류와 용도를 나타낸 것이다(Setiati et al., 2018).
Table 1.
Required HLB value for multiple applications (Setiati et al., 2018)
유화산은 염산의 낮은 점성도를 보완하기 위해 염산에 오일과 유화제를 첨가하여 점성도를 높인 것으로 저류층에 주입하는 유체의 주입률을 낮출 수 있다. 이러한 특징은 산과 암체 사이의 체적접촉효율을 증가시키고 투과도가 불균질한 탄산염암 저류층에서 투과도가 낮은 지층까지 골고루 산처리 공법을 수행할 수 있게 한다(Jafarpour et al., 2019). 하지만 점성도가 증가하면 주입압력이 지층의 파쇄압 이상으로 상승하는 문제점이 발생하여, 유화산의 점성도에 대한 이해가 필요하다(Daeffler et al., 2018). 유화산은 전단응력(shear stress)과 전단속도(shear rate)의 관계가 일정하지 않은 비뉴턴유체(non-Newtonian fluid)이다. 전단속도가 증가할수록 점성도가 감소하는 전단감소(shear thinning) 현상이 나타나며, 이는 식 (1)과 같이 나타낼 수 있다(Sayed and Nasr-El-Din, 2013). 따라서, 유화산의 겉보기 점성도(apparent viscosity)는 전단속도와 함께 제시되어야 하고, 일반적으로 유화산은 전단속도가 10 s-1일 때 겉보기 점성도는 약 100 cp, 전단속도가 1000 s-1일 때 겉보기 점성도를 약 10 cp를 갖는다(Sayed et al., 2013; Cairns et al., 2016).
µ= apparent fluid viscosity, poise
k = power-law consistency factor, g/cm·s(2-n)
γ = shear rate, s-1
n = power-law index
또한, 탄산염암 저류층에 유화산 주입 시 유화산의 안정성과 산-암석 반응을 필수적으로 고려해야 한다. 따라서 효율적인 웜홀을 형성하기 위해서는 목표 저류층에 적합한 유화산을 제조하고 유화산 산처리 공법의 핵심 메커니즘을 분석하는 것이 필요하다.
유화산의 제조 및 안정성 평가
유화산 제조
유화산은 경제적이고 손쉽게 구할 수 있는 재료를 활용할 수 있어 준비 절차와 제조가 간단하다. 일반적으로 W/O 유화산은 염산에 오일, 유화제, 철-제어제, 부식방지제를 혼합하여 제조한다(Carins et al., 2016). 암체 산처리 공법에서 사용되는 염산은 보통 15%의 농도를 사용하며, 이때 부식방지제와 같은 첨가물들이 최대의 호환성을 발휘한다(Al-Mutairi et al., 2009; Hong et al., 2018). 하지만 유화산을 사용하는 산처리 공법은 고온에서도 염산의 강한 반응성을 보호할 뿐만 아니라 생산설비의 부식성을 낮출 수 있어 비교적 고농도(20~28%)의 염산을 사용할 수 있다(Al-Mutairi et al., 2009; Jafarpour et al., 2019). 염산의 빠른 반응성을 지연시키기 위해 확산장벽으로 디젤(diesel)을 일반적으로 사용하며, 현장에서 생산된 원유를 활용하여 경제적인 제조도 가능하다(Kasza et al., 2006). 산-오일 비율(acid-oil ratio)은 70:30이 주로 사용되며, 이는 산의 비율을 최대로 유지하면서 유화산의 안정성이 오랫동안 지속되는 최적의 비율로 알려져 있다. 이때, 오일의 비율이 높아질수록 유화산의 점성도가 낮아지고 액적 크기 또한 작아지는 경향이 있다(Xiong et al., 2010; Zakaria and Nasr- El-Din, 2016).
유화산을 제조함에 있어 가장 중요한 첨가제는 유화제이다. 유화산의 액적 크기와 형태, 안정성 등을 포함한 물리적 성질은 유화제의 종류, HLB 값, 첨가량에 따라 결정된다. 유화제의 종류는 헤드의 이온성에 따라 세 가지로 나뉜다. 양이온성 유화제는 다중 사슬구조로 시간에 따른 유화산의 안정성을 높이는 특징이 있으며, 양이온을 띄는 탄산염암에 흡착이 적어 유화산 제조에 자주 사용된다(Nasr-El-Din et al., 2001). 또한 저류층 내에서 탄산염암에 흡착된 오일을 탈착시킴으로써 친유성인 탄산염암의 습윤도(wettability)를 친수성으로 변환시키는 성질이 있다. 하지만 양이온성 유화제는 대개 HLB 값이 높아 O/W 에멀젼을 형성하기 때문에 HLB 값이 낮은 비이온성 유화제와 혼합하여 사용하기도 한다. 음이온성 유화제는 탄산염암 저류층에 흡착하는 성질 때문에 음이온을 띄는 사암 저류층에 주로 사용되며, 보통 양이온성 유화제나 비이온성 유화제와 혼합하여 사용된다(Jarrahian et al., 2012). 비이온성 유화제는 직선형 사슬구조 형태로 HLB 값의 범위가 넓어 다양한 형태의 에멀젼을 제조하는데 널리 사용되며 고온에서 에멀젼의 안정성을 증가시키는 성질이 있다(Alabdulmohsen, 2015). 또한, 서로 다른 두 종류 이상의 유화제를 HLB 값이 3~6이 되도록 혼합하여 사용할 때 W/O 유화산이 형성되고 시간에 따른 안정성이 높아지게 되므로 혼합 유화제의 사용에 대한 연구가 필요하다(Yeon et al., 2014; Mohamed et al., 2017; Choi and Jin, 2019). 또한 유화제의 첨가량이 증가할수록 유화산의 점성도가 증가하고 액적 크기는 작아지는 경향이 있어 유화산 제조 후 안정성 평가(stability test)를 통해 유화제의 종류와 적절한 첨가량을 도출해야 한다(Al-Mutari et al., 2007; Sidaoui and Sultan, 2016).
산처리 공법에 사용되는 염산은 생산설비를 부식시키는 성질이 있어 부식방지제와 철-제어제가 일반적으로 첨가된다. 하지만 유화산은 디젤이 염산과 생산설비가 직접 접촉하는 것을 막아 부식방지제와 철-제어제의 첨가가 최소화 되거나 첨가하지 않기도 한다(Nasr-El-Din et al., 1999).
안정성 평가
유화산을 제조한 후 액적 시험(droplet test)과 상분리 시험(separation test)을 진행하여 유화산의 안정성을 평가한다. 먼저 유화산의 형태를 확인하는 액적 시험을 수행하여 탄산염암 저류층에 주입하기 적합한 W/O 유화산이 형성됨을 확인한다. 유화산 액적을 물에 떨어뜨렸을 때, Fig. 5의 (a)와 같이 물에서 분리되지 않고 액적 모양을 그대로 유지할 때 W/O 유화산이 형성된 것으로 판단한다(Sidaoui and Sultan, 2016; Mohamed et al., 2017; Sokhanvarian et al., 2019). 반대로 (b)와 같이 유화산 액적이 물에 풀어지면 O/W 유화산이 형성된 것으로, 이는 유화산 산처리 공법에 적합하지 않다.
W/O 유화산의 형성이 확인되면, 상분리 시험을 통해 온도와 시간에 따른 상대부피(relative volume)를 측정하고 유화산의 안정성을 파악한다(Sidaoui and Sultan, 2016). 현장적용에 있어 염산과 오일의 분리를 방지하기 위해 유화산의 온도와 시간에 대한 안정성 파악은 매우 중요하다(Nasr-El-Din et al., 1999). 상대부피는 전체 유체의 부피(total volume)에 대한 안정한 유화산(phase volume)의 부피의 비율을 나타낸 것으로, 식 (2)와 같이 나타낼 수 있다. 유화산은 제조 직후부터 운반을 위한 상온(25°C)에서 24시간, 저류층 주입을 위한 고온(70°C 이상)에서 4시간 이상 상대부피가 95% 이상으로 유지될 때 안정한 유화산이라고 판단한다(Mohamed et al., 2017; Sidaoui et al., 2018).
Fig. 6은 시간에 따른 유화산의 상대부피를 측정한 것이다. 그림 (a)는 유화산의 제조 직후이며, (b), (c)와 (d)의 순서로 일정 시간의 경과에 따른 유화산의 형태를 나타낸다. 이때, (a)와 (b)는 상대부피가 95% 이상 유지되어 안정한 유화산으로 평가 될 수 있으며, (c)와 (d)는 에멀젼의 상분리가 일어난 상태이므로 불안정한 유화산이라 판단된다. 따라서 시간이 지남에 따라 유화산 내의 오일과 염산이 분리되며, 상대적으로 W/O 에멀젼의 상대부피가 감소하는 것을 알 수 있다.
유화산 산처리 공법 메커니즘
암체 산처리 공법을 통해 형성되는 웜홀의 직경, 길이, 분포와 같은 형태가 유정의 생산성에 큰 영향을 미친다(Yoo and Lee, 2018). 웜홀의 형태는 산과 암석의 반응에서 산의 확산계수와 주입률에 의해 결정되고, 이를 도출하기 위해 유화산과 탄산염암 사이의 반응 과정에 대한 분석을 수행한다. 탄산염암의 주 구성요소는 탄산염(CO32-)이며, 칼슘 이온(Ca2+) 및 마그네슘 이온(Mg2+) 등과 결합한 상태로 존재한다. 염산과 탄산염암의 반응식은 식 (3)과 식 (4)와 같이 나타낼 수 있다.
확산계수는 산과 암석간의 고유한 반응 특성으로, 암체 산처리 공법 설계 시 유체의 최적 주입조건을 설계하는데 사용되는 필수적인 인자이다. 확산계수를 산출하기 위해 대표적으로 회전식 디스크(rotating disk apparatus, RDA) 실험을 수행하며, Fig. 7의 (a)는 RDA 실험 장치의 모식도이다(Taylor et al., 2004; Taylor and Nasr-El-Din, 2007, Reyath et al., 2015; Yoo et al., 2019). RDA 실험은 제한된 물질 이동 상태를 묘사하여 물질의 이동 속도와 관련성이 있는 용해도 및 확산계수를 측정하는 실험으로, 반응기에 암석 디스크를 장착한 후 산 용액을 주입하고 디스크를 회전 시켜 반응을 유도하는 원리이다. 일정한 시간 간격으로 암석과 반응한 샘플을 채취하고 샘플 내 이온 분석(Ca2+, Mg2+)을 통해 암석의 용해도와 확산계수를 얻는다. Fig. 7의 (b)와 같이 RDA 실험을 통해 반응 시간에 따른 칼슘 이온과 마그네슘 이온 농도를 그래프로 도시한 후 기울기를 산출한다. 이때 그래프의 기울기를 암석 디스크의 표면적으로 나누어 용해도를 구할 수 있으며, 암석 디스크의 표면적은 식 (5)와 같이 나타낼 수 있다.
A = the initial surface area of the disk, cm2
Ac = the disk cross-sectional area, cm2
φ = the initial porosity of the disk
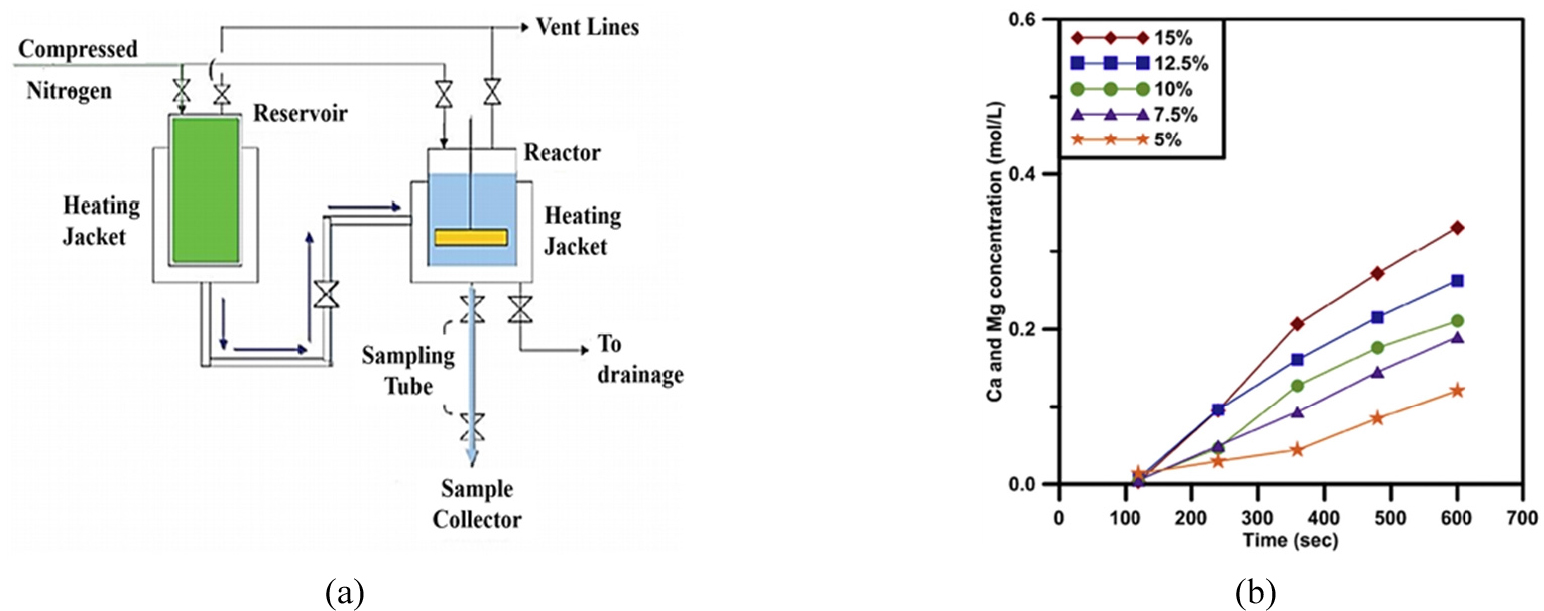
Fig. 7.
(a) Schematic diagram of rotating disk apparatus (Reyath et al., 2015), (b) Ca and Mg ions concentration (Yoo et al., 2018).
유화산을 사용한 RDA 실험은 암석 표면에서 반응물의 확산이 표면 반응속도보다 느린 제한된 물질 이동상태(mass transfer limited regime)일 때 이루어지며, 용해도는 식 (6)과 같이 나타낼 수 있다.
JH+ = the mass transfer rate of H+ from the bulk to the disk, moles/cm2·s
kmt = the mass transfer coefficient, cm/s
Cb = the concentration of H+ in the solution, mole/cm3
Cs =the concentration of H+ in the core surface, mole/cm3
여기서 물질 이동 계수인 kmt는 de Rozieres et al.(1994)이 제안한 식 (7)과 같이 나타낼 수 있으며, 비뉴턴유체의 확산계수 D로도 표현이 가능하다. 이때, 멱급수 점조도지수(power-law consistency factor) k와 멱급수 지수(power-law index) n은 비뉴턴유체의 점성도를 구하는 식 (1)에서 구할 수 있다.
φ(n) = an empirical function
D = diffusion coefficient, cm2/s
ρ = the fluid density, g/cm3
a = disk radius, cm
ω = the disk rotational speed, rad/s
RDA 실험을 통해 얻은 용해도와 식 (7)을 이용하여 확산계수를 산출할 수 있으며, 제시된 산-암석 반응 분석 방법은 유체의 특성과 실제 산-암석 반응 실험결과를 적용하여 정확도가 매우 높다(Yoo et al., 2018).
암체 산처리 공법에서 최적 주입률은 목표 길이의 웜홀을 형성하는데 필요한 산의 양이 최소가 될 때의 주입률을 의미하며, 이때 공법의 효율이 극대화된다. 즉, 동일한 양의 산을 주입할 경우 최적 주입률 조건에서 웜홀이 가장 깊이 형성될 수 있다. 최적의 웜홀을 형성하기 위해서는 최적 주입률 산출에 대한 연구가 진행되어야 하며, 주로 산처리 코어유동 실험을 통해 이루어진다. Fig. 8의 (a)는 산처리 코어유동 실험장치의 모식도이며, 산처리 코어유동 실험은 코어 내에 일정한 속도로 산을 주입하여 산이 주입되는 시점부터 시간에 따른 주입부와 배출부의 압력 차를 통해 코어 내 돌파(breakthrough)가 일어난 시간을 측정한다. 웜홀이 생성된 시간과 산의 주입속도를 이용하여 산의 총 주입량을 계산하고, 코어 공극부피(pore volume)로 나누어 산처리 공법의 효율을 나타내는 지표인 무차원 돌파지수(pore volume to breakthrough, PVBT)를 산출한다. 이때 저류층의 온도 및 압력 조건에서 산의 주입률을 달리하여 여러 차례의 코어유동 실험을 진행하고, 산출한 PVBT를 (b)와 같이 그래프로 도시하여 가장 낮은 PVBT를 나타낸 주입률을 최적 주입률로 선정한다(Fredd and Fogler, 1998; Al-Harthy et al., 2009; Yoo and Lee, 2019).
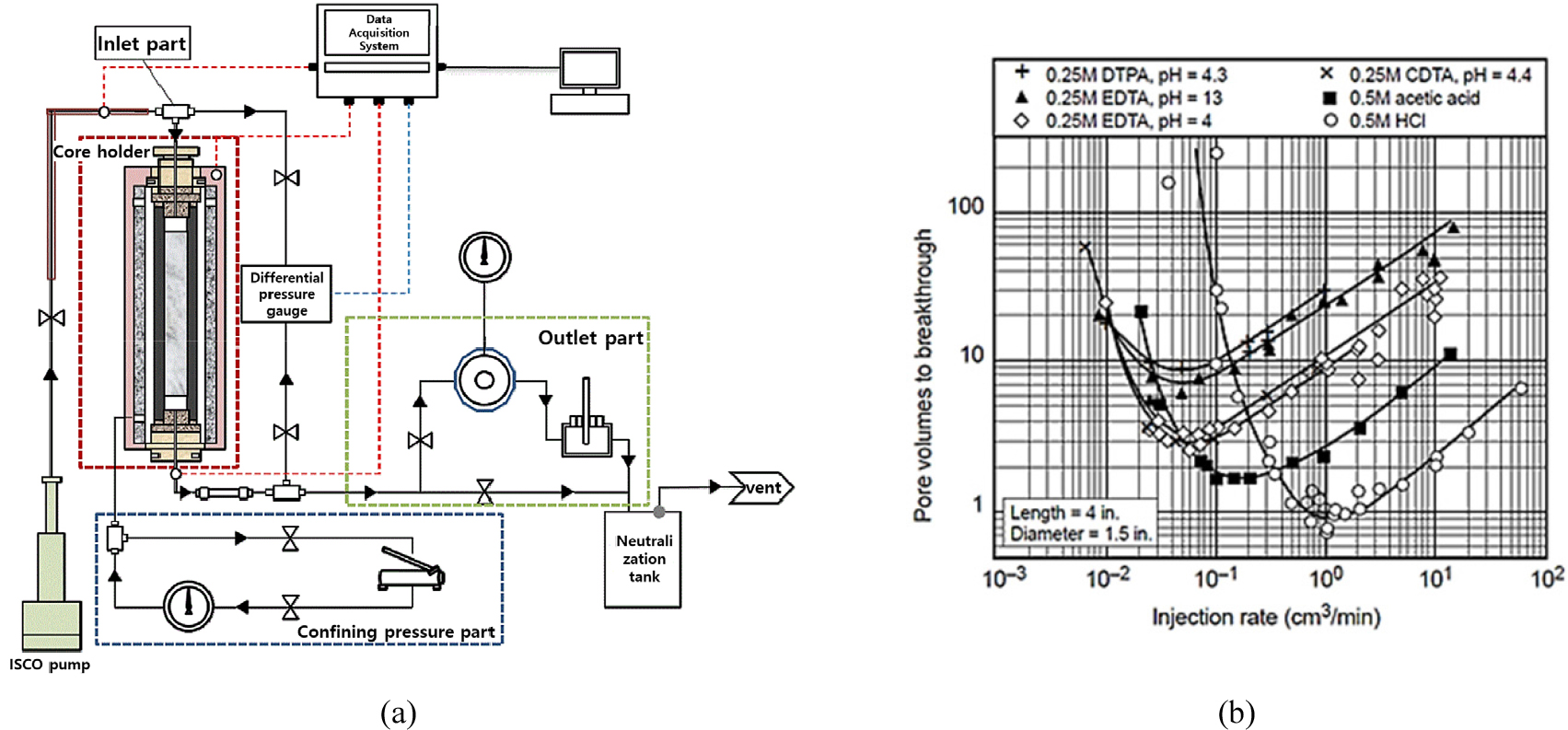
Fig. 8.
(a) Schematic diagram of matrix acidizing system (Yoo and Lee, 2019), (b) Pore volume to breakthrough by the injection rate with various stimulation fluids at 22°C (Fredd and Fogler, 1998).
현장 적용사례 분석
Sungai Kenawang 가스전
Sungai Kenawang 유전은 Fig. 9와 같이 인도네시아의 남수마트라 Jambi Merang 분지의 북쪽에 위치하고 있으며, 주요 생산 저류층은 석회이암(lime-mudstone), 와케스톤(wackestone), 석회입자암(lime-grainstone)이 주를 이루고 있는 Baturaja 지층이다(Madyanova et al., 2012; Petrominer, 2019). 심도 7,000 m에 위치한 저류층의 온도는 최대 176°C이며, 투과도는 10~350 mD, 공극률은 10~17%로 불균질한 성질을 가지고 있는 고온 불균질 가스저류층 적용사례이다.
Talisman사와 Schlumberger사는 Sungai Kenawang 유전 중 SKN-A 유정의 시추액에 의한 유정손상을 개선하기 위해 15% 염산을 사용한 겔화산을 이용하여 암체 산처리 공법을 진행하였다. 하지만 공법의 수행결과 유정손상지수(skin)가 +19에서 +14로 감소하여 유정손상의 개선이 효과적으로 이루어지지 않았다. 따라서 SKN-A 유정에는 15% 염산을 단독으로 사용하여 암체 산처리 공법을 다시 진행하였다. 또한, SKN-B 유정에는 염산과 고온의 탄산염암 사이의 강한 반응을 방지하는 효과를 가지며, 높은 점성도로 인해 저류층 전반적으로 산처리 공법을 수행할 수 있는 유화산을 사용하여 산처리 공법을 진행하였다. 현장 수행에 앞서 SKN-B 유정의 코어를 사용하여 X선 회절(X-ray diffraction, XRD)분석을 통해 코어의 광물학적 분석을 수행하였으며, 현장 시료는 95% 이상이 탄산염암으로 이루어져 있음을 확인하였다. 유화산은 15%의 염산과 디젤의 비율을 70:30으로 0.6%의 유화제와 3%의 부식방지제, 1%의 철 제어제를 혼합하여 제조하였다. 제조된 유화산은 상온에서 3시간, 고온에서 1.5시간 이상의 시간에 따른 안정성을 확보하였으며, 상온에서 82 cp(170 s-1)의 점성도를 보였다.
Sungai Kenawang 유전의 SKN-A 유정과 SKN-B 유정의 산처리 공법 수행결과는 Table 2와 같다. 염산을 사용하여 산처리 공법을 수행한 SKN-A 유정의 오일과 가스의 유동량(Qg, Qo)은 약 2배 이상, 유화산을 사용하여 산처리 공법을 수행한 SKN-B 유정은 약 3배 이상 개선되어 두 공법 모두 성공적임을 보였다. Fig. 10은 두 유정의 개선된 생산성을 비교한 것으로, 염산을 사용하여 공법을 진행한 SKN-A 유정은 지층의 상부를 중심으로 투과도 개선이 이루어졌다. 반면에 유화산을 사용한 SKN-B 유정은 상부와 하부 모두 생산량이 증가하여 저류층의 투과도가 전반적으로 개선되었다(Madyanova et al., 2012). 따라서 고온의 불균질한 가스저류층에서 겔화산을 사용할 경우 저류층의 투과도 개선에 실패하여 추가적인 공법을 수행해야 하지만 유화산의 경우 단번의 공법 수행으로도 성공적으로 저류층 개선이 가능하다. 또한 투과도 범위가 넓은 저류층의 전반적인 개선을 위해서는 유화산을 적용하는 것이 효율적인 것으로 판단된다.
Table 2.
Well performance of SKN-A and SKN-B before and after stimulation (Madyanova et al., 2012)
BMB 유전
BMB 유전은 Fig. 11과 같이 폴란드 북서부에 위치하고 있으며, 백운암이 주성분인 탄산염암으로 구성되어 있다(Jedrzejowska et al., 2004; Kasza et al., 2006). 심도 약 3,000 m에 위치한 저류층의 초기 압력은 약 8,000 psi이며, 평균 온도는 약 120°C, 투과도는 9~28 mD, 평균 공극률은 14%인 고압의 오일저류층 적용사례이다. BMB 유전은 2000년 3월부터 생산이 시작되었으나 유정 주변의 높은 손상 때문에 오일과 가스의 생산량이 낮아 염산과 아세트산(acetic acid)를 혼합하여 산처리 공법을 진행하였다. 하지만 고온의 저류층에서 탄산염암과 산의 빠른 반응성으로 인해 유정의 투과도을 개선하는데 실패하였다. 따라서 탄산염암과 산의 빠른 반응성을 보완하고 효율적인 웜홀을 형성하여 유정의 투과도를 개선하기 위해 유화산을 사용한 산처리 공법을 진행하였다.
염산 15%에 생산한 원유를 1:1 비율로 혼합하고 2%의 유화제와 0.2%의 부식방지제를 첨가하여 유화산을 제조하였으며, 저류층의 고온·고압 조건에서 3시간 이상 안정함을 보였다. 현장 적용에 앞서 BMB 유전의 코어와 유화산을 사용하여 120°C에서 RDA 실험과 산처리 코어유동 실험을 진행하였다. 실험 결과, 염산 15%보다 유화산 사용 시 생성된 웜홀의 길이와 형태가 더 우수함을 확인하였다(Kasza et al., 2006). BMB 유전의 오일 유정인 Ba-5, Bu-9, Bu-17에 유화산 산처리 공법 적용 결과는 Table 3과 같다(Kasza et al., 2006). 유화산 산처리 공법 수행 전, 후 비교 결과, 오일의 유동량(Q)은 약 1.2~1.4배의 개선을 보였으며, 생산성 지수(productivity index, PI)는 2배에서 최대 13배까지 증가함을 보였다. 또한, Table 3에서 는 저류층 압력과 공저 압력(bottom-hole pressure)의 차를 나타내며, 유화산 산처리 공법 후 저류층 내의 가 감소하는 것을 보아 투과도 개선이 효과적으로 이루어짐을 확인할 수 있다. 특히, 공법 수행 후 모든 유정에서 오일의 유동량과 생산성지수(productivity index, PI)가 전반적으로 증가하였으므로 고온·고압 저류층의 유정손상을 개선하기 위해서는 염산과 아세트산을 혼합하여 사용하는 것보다 산과 암석의 반응성을 지연시키는 효과를 가진 유화산을 사용하는 것이 효율적이다.
Table 3.
Production performance of BMB oil wells before and after stimulation (Kasza et al., 2006)
Mumbai High 유전
Mumbai High 유전은 Fig. 12와 같이 인도 서부 연안에 위치하고 있다(Moitra et al., 2007). 주요 생산 저류층은 석회암과 셰일로 이루어져 있는 신생대 제 3기의 불균질한 탄산염암이 2~4개의 층으로 생성되어 있으며, 투과도의 범위는 5~500 mD로 투과도 편차가 큰 다층(multi-layered) 저류층 적용사례이다(Sarma et al., 2012). 1974년에 발견되어 1976년 생산을 시작한 Mumbai High 유전은 Oil & Natural Gas Corporation(ONGC)사에 의해 개발되었다.
해당 유전은 각 층의 높은 투과도 편차로 인해 저류층의 생산량이 낮은 문제가 있어 유정의 생산성을 개선하기 위한 암체 산처리 공법을 진행하였다. 하지만 투과도 편차가 큰 저류층에서 염산만을 사용하여 암체 산처리 공법을 수행하게 되면 투과도가 높은 지층으로만 유체가 흐르게 되어 저류층의 투과도를 부분적으로만 개선하여 공법이 실패하는 문제가 발생하였다. 따라서 저류층의 전반적인 투과도 개선을 위하여 투과도가 낮은 지층부터 투과도가 높은 지층까지 유체가 균일하게 주입할 수 있는 산 혼화 기법이 필요하였다. Mumbai High 유전에서는 염산 15%에 0.75%의 겔화제(hydroxyethyl cellulose, HEC), 0.75%의 잔탄검(xanthan gum), 2%의 유화제와 오일을 혼합하여 SDA(self- diverting acid)를 제조하였다(Sarma et al., 2012). Fig. 13의 (a)는 Well A2의 생산 이력을 나타낸 결과로 SDA 산처리 공법 적용 이후 오일의 생산량이 약 100 bopd에서 300 bopd까지 3배 이상 증가하였으며, 개선된 생산량이 지속적으로 유지되었음을 보여준다(Sarma et al., 2012). Fig. 13의 (b)는 Well A16의 생산 이력을 나타내며, 공법 적용 이후 오일의 생산량이 약 480 bopd에서 650 bopd까지 1.3배 이상 증가하였다. 또한, 물 생산율(water cut)이 감소하거나 일정하게 유지됨을 보아 전체 유체의 생산량 증가는 오일의 생산량 증가가 원인임을 알 수 있다. 따라서 투과도의 편차가 큰 다층 저류층을 개선하고자 할 때 혼화산을 사용하여 암체 산처리 공법을 수행하는 것이 효과적이다.
결 론
본 연구에서는 탄산염암 저류층에서 유화산을 이용한 산처리 공법 기술 특성 및 메커니즘을 분석하였고 현장사례를 조사하였다. 이를 통해 얻은 결론은 다음과 같다.
(1)유화산을 이용한 암체 산처리 공법은 오일의 확산장벽으로 인해 염산과 탄산염암 사이의 강한 반응성과 생산 설비에 대한 부식을 방지함으로써 효율적인 공법 수행이 가능하며, 치밀 탄산염암 저류층에서 폴리머산과 겔화산의 주입문제를 보완하는데 효과적이다.
(2)성공적인 유화산 산처리 공법 수행을 위해서는 안정성 평가를 통해 상온과 고온 조건에서 시간에 따른 안정성을 확보한 W/O 유화산이 제조되어야 하며, 공법 설계 시 RDA 실험 및 산처리 코어유동 실험을 통해 유화산과 탄산염암 사이의 반응 메커니즘을 분석하고 최적 주입률을 선정하는 것이 필요하다.
(3)현장사례 분석 결과, 유화산 산처리 공법은 고온의 불균질한 탄산염암 저류층에서 염산의 빠른 반응성을 보완하여 수배의 유정 개선 효과를 나타냈으며, 투과도 편차가 큰 다층 저류층에서도 생산성을 전반적으로 개선하는데 용이함을 확인하였다.
(4)제시된 유화산 산처리 공법 기술 특성 및 메커니즘과 현장사례는 향후 탄산염암 저류층에서 유화산 산처리 공법을 적용한 유정의 생산성 개선 프로젝트의 설계를 위해 기초자료로 활용될 수 있을 것으로 사료된다.